Save Money with Professional Packaging Machine Repair and Maintenance
Quick and Reliable Product Packaging Maker Repair Service Services to Minimize Downtime
In the affordable landscape of manufacturing, the effectiveness of product packaging operations pivots on the dependability of equipment. Quick and reputable repair work solutions are crucial in minimizing downtime, which can lead to substantial functional problems and economic losses. Understanding the value of prompt treatments and the function of specialist specialists can transform just how companies come close to repair and maintenance. Nonetheless, browsing the myriad alternatives offered for repair service services can be challenging. What elements should companies take into consideration to guarantee they are making the right selection for their functional needs?
Significance of Timely Repair Works
Prompt repairs of packaging devices are critical for keeping operational performance and lessening downtime. In the fast-paced environment of production and product packaging, also small malfunctions can lead to significant hold-ups and performance losses. Dealing with issues promptly makes certain that makers operate at their optimal capacity, therefore safeguarding the circulation of procedures.
Moreover, regular and timely upkeep can protect against the rise of small issues right into significant failures, which often incur greater repair work prices and longer downtimes. An aggressive strategy to machine repair service not only maintains the integrity of the devices yet likewise boosts the overall integrity of the manufacturing line.
Additionally, timely repairs contribute to the long life of product packaging equipment. Machines that are serviced immediately are less likely to struggle with excessive wear and tear, enabling services to optimize their investments. This is specifically important in markets where high-speed packaging is crucial, as the demand for constant efficiency is vital.
Advantages of Reliable Provider
Reliable service providers play a crucial duty in guaranteeing the smooth operation of product packaging makers. Their knowledge not only boosts the effectiveness of repair services yet also adds considerably to the durability of equipment.

Furthermore, a reputable provider offers thorough assistance, including training and assistance for team on machine procedure and upkeep finest techniques. This not only empowers workers but likewise grows a society of safety and efficiency within the company. In general, the benefits of involving reputable provider prolong beyond immediate repair work, favorably influencing the entire functional operations of product packaging procedures.
Common Product Packaging Machine Problems
In the realm of product packaging operations, numerous problems can compromise the efficiency and capability of equipments (packaging machine repair). Another typical issue is misalignment, which can create jams and uneven packaging, influencing product top quality and throughput.
Electric problems can likewise disrupt packaging procedures. Malfunctioning circuitry or malfunctioning sensing units might lead to irregular equipment behavior, triggering hold-ups and look at here boosted functional prices. Furthermore, software program problems can hinder the equipment's programming, leading to functional ineffectiveness.
Inconsistent item flow is another vital concern. This can occur from variations in product form, weight, or dimension, which may get redirected here affect the equipment's capability to handle products accurately. Inadequate training of drivers can aggravate these troubles, as untrained employees may not acknowledge early signs of breakdown or may misuse the tools.
Dealing with these usual packaging maker concerns quickly is important to keeping performance and making sure a smooth operation. Normal assessments and aggressive maintenance can dramatically mitigate these concerns, cultivating a reliable packaging atmosphere.
Tips for Minimizing Downtime
To reduce downtime in packaging operations, implementing a positive upkeep strategy is critical. On a regular basis arranged maintenance checks can identify potential issues prior to they intensify, guaranteeing equipments run successfully. Developing a regimen that includes lubrication, calibration, and examination of crucial parts can dramatically decrease the regularity of unforeseen malfunctions.
Training personnel to operate equipment properly and recognize early indication of malfunction can additionally play an essential function. Equipping drivers with the understanding to carry out standard troubleshooting can avoid minor issues from causing significant delays. Preserving an efficient stock of essential extra components can accelerate repair work, as waiting for parts can lead to prolonged downtime.
Additionally, documenting maker performance and upkeep activities can aid identify patterns and reoccurring troubles, allowing for targeted interventions. Incorporating advanced tracking modern technologies can provide real-time data, enabling predictive maintenance and lessening the danger of unexpected failings.
Lastly, fostering open interaction in between drivers and maintenance groups guarantees that any abnormalities are immediately reported and resolved. By taking these proactive measures, companies can improve functional effectiveness and significantly reduce downtime in packaging procedures.
Choosing the Right Repair Service
Picking the ideal repair service for packaging equipments is a vital choice that can considerably affect operational performance. Begin by assessing the service provider's experience with your particular type of product packaging devices.
Next, consider the solution provider's online reputation. Seeking comments from various other organizations within your market can supply understandings right into integrity and quality. Accreditations and partnerships with identified devices suppliers can also indicate a dedication to quality.
In addition, examine their response time and schedule. A company who can offer prompt assistance lessens downtime and maintains manufacturing circulation stable. It's additionally vital to make inquiries concerning service warranty and service guarantees, which can reflect the confidence the supplier has in their job.

Verdict
In verdict, the significance of quick and reputable product packaging machine fixing solutions can not be overstated, as they play a critical duty in minimizing downtime and making certain operational efficiency. Carrying out proactive upkeep practices and spending in staff training more boosts the durability of packaging machinery.
Prompt fixings of product packaging makers are vital for keeping operational performance visit here and lessening downtime.Furthermore, timely repair work contribute to the long life of packaging equipment. Generally, the advantages of involving reputable solution suppliers expand past immediate repair services, favorably affecting the entire functional process of packaging processes.
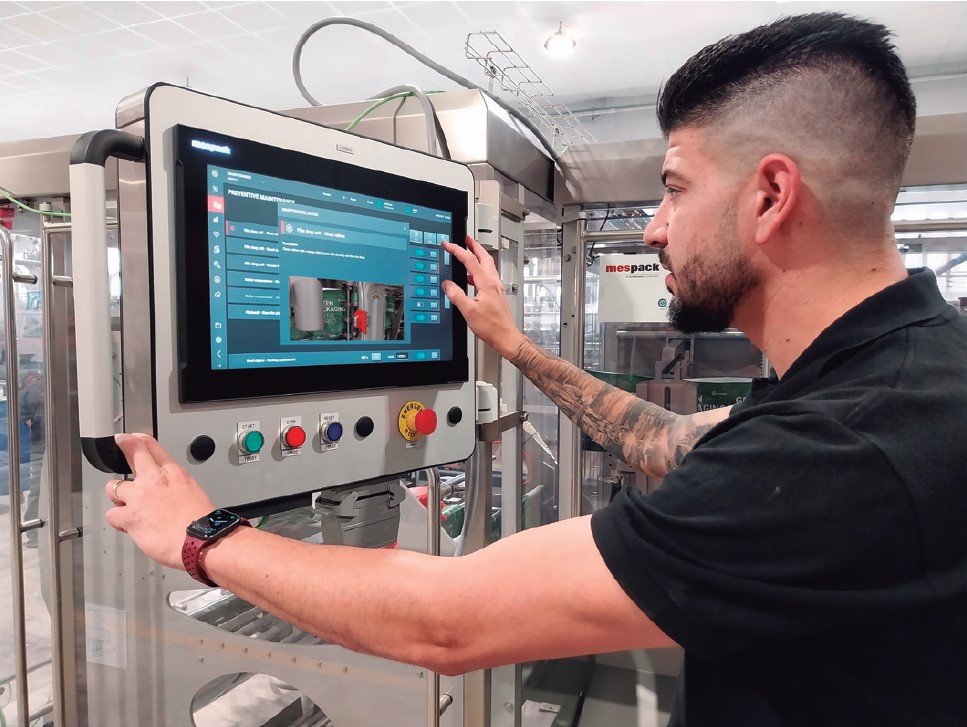